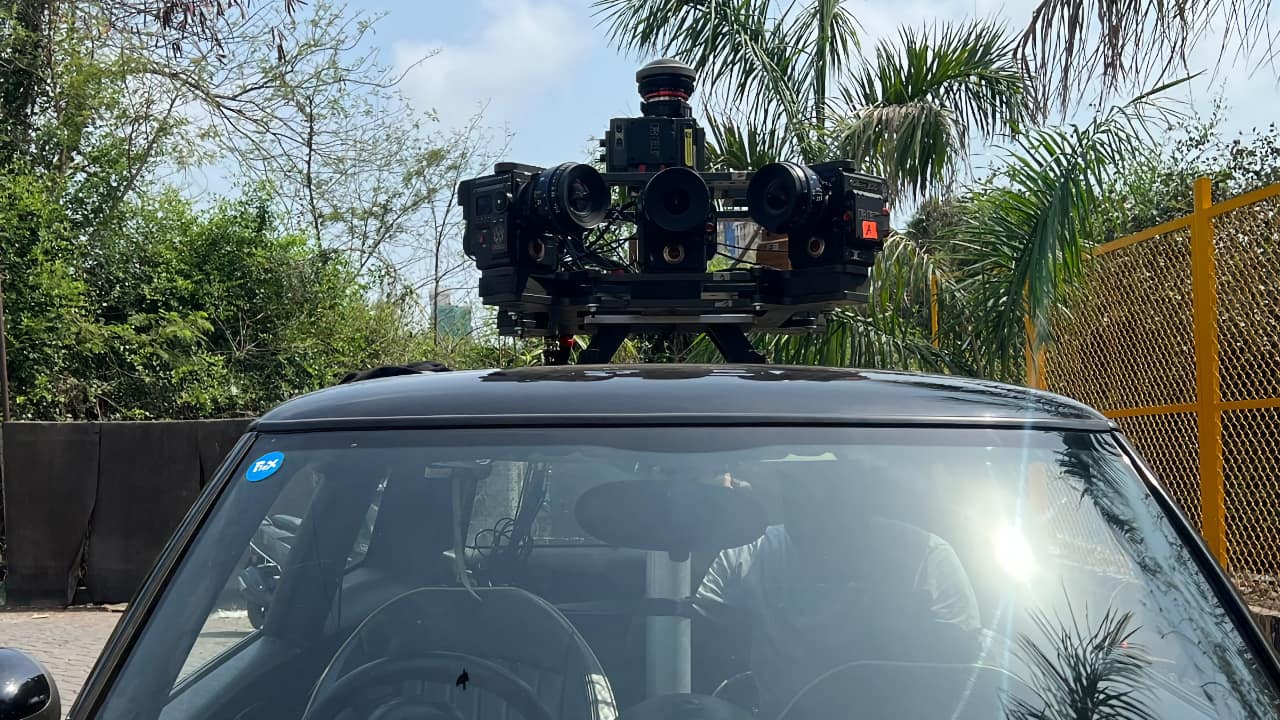
Some scenes need bespoke kit to make them really work properly, as India’s Futureworks found out when it came time to deliver some high-profile driving dialogue scenes for Netflix.
Not too much bothers the experienced VFX super nowadays, but there are always several types of scenes that can trip up even a well-resourced production with a decent budget. CG humans and creatures interacting are perennially difficult — think of any number of scenes where formerly convincing Character A suddenly mounts horse/dragon/alien B and you can almost hear the suspension of disbelief shattering in the cinema — and so too, oddly enough, are driving dialogue scenes.
We were watching Interstellar recently, for instance, which is not exactly known for its shoddy VFX, when in the Earth-bound start there’s a brief cut in a driving dialogue scene that’s so obviously greenscreen it’s painful. The thing is, they’re difficult to do. Even with the all-singing all-dancing LED volumes increasingly ruling the driving dialogue roost these days, the background plates sitll have to be shot.
Which brings us to our story…
When India-based post-production studio, FutureWorks, was challenged with delivering the VFX for a dialogue-driving scene, it faced an ever-present obstacle in producing a realistic sequence. The traditional technique adopted in the past was to use green screens where they would record multiple camera angles with the DoP having to shoot a separate plate for each angle. All of the shots and plates would then be comped together into the final video.
Gouri Shankar, VFX Supervisor at FutureWorks explains that: “This workflow has a number of inherent challenges, including potential inconsistencies between angles, unrealistic reflections, and a lot of extra work on set.” FutureWorks began to think about whether there was a different approach that would eliminate these issues and create better results for their clients.
The idea gripped the team such that they began to develop the idea and create a working prototype. As there was no off-the-shelf solution that could be purchased for this and no previous rig that suited the specific needs of the shoot, they needed to create a bespoke setup that worked exactly as they needed it to.
The primary challenge was to work out how much overlap was required between the shots to enable a natural looking field of view no matter which part of the 360-degree plate they ended up using. “Our team analysed footage and utilised Unreal Engine to replicate these ideas in a virtual world, all the while testing the results and fine-tuning the rig.” Shankar continues. “This process enabled us to have a lot more confidence once they were ready to start building the rig.”
Building the prototype
The first physical prototype involved creating a wooden frame that would be the correct structure for housing the cameras and their lenses. This rig was created based on the analysis that had been carried out in Unreal Engine. Only three cameras were used in the initial iteration of the design but that was all they needed to enable the team to further analyse the footage and revise their plans. This additional step meant FutureWorks could optimize the positioning of the cameras and help to ensure the most accurate solution was found.
FutureWorks landed on a nine-camera setup with eight cameras covering 360 degrees horizontally and a single camera covering the sky. All nine cameras were RED DSMC2 Helium bodies with eight of them paired with the 21mm Zeiss CP3 lens. The ninth camera pointing upwards to zenith used a 6mm fisheye lens. FutureWorks found that using top-quality lenses was vitally important to minimize distortion in the resulting footage, something that would have made the stitching process more difficult.
The camera positions gave FutureWorks a 30% overlap Field of View (FOV) between adjacent shots and the whole thing resulted in a stitched image of 23,000px by 4,200px.
All of these cameras and lenses were sourced through the FutureWorks rental team, making the overall process of supplying the required kit as smooth as possible. The actual physical structure housing the camera equipment was made from aluminium and was completely bespoke, with no products bought off the shelf. The rig was built by the rental team, headed up by Nitin Yadav, Technical Head of Department at FutureWorks Rental.
Going live
With the rig fully tested and built, it then came time to actually use the rig on a live production. It was initially used on a number of shows for leading streaming services, and the results were highly authentic. One of the immediately obvious benefits was the speed at which the photography team could shoot a whole driving sequence. Having to only capture one single shot, rather than multiple, drastically simplified everything on set. It also meant that all the footage was captured at the same time of the day, something that couldn’t be guaranteed when working with multiple different angles and plates.
It wasn’t just the DoP that had an easier time of it though, when the VFX team received the footage, they had to do a lot less work to composite it all together. As a result, the whole thing could be turned around in a much quicker timeframe.
Alongside the speed improvements, FutureWorks has also been able to produce dramatically better results. “The 360 degree view enables a more accurate interaction with the environment and continuity of reflection with the background plate,” Shankar says. “The setup gives a more realistic reflection pass with exact contours of the car body as well as accurate reflections from the sky. This all results in a much more convincing final result.”
Tags: Post & VFX
Comments