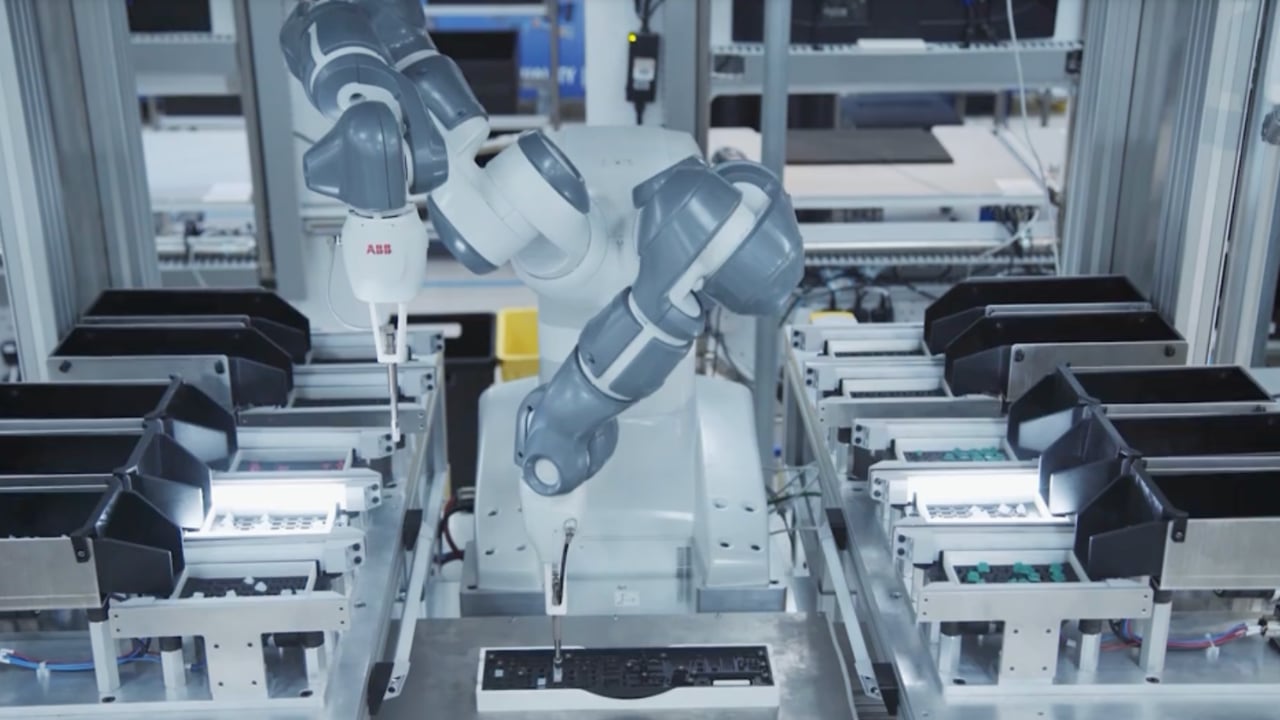
David Shapton visits the Sony Pencoed Technology Centre in Wales, home to one of the most advanced manufacturing environments in the world, and the new Sony HXC-FZ90.
China, South Korea, Japan, Taiwan, and Wales. Can you spot the odd one out? The first four countries are technology innovators and cutting-edge electronic manufacturers. Wales? You might be surprised to hear it's also a technology innovator and cutting-edge electronic manufacturer.
Nestling in the Vale of Glamorgan in Wales, the Sony Pencoed Technology Centre is home to one of the most advanced manufacturing environments in the world. It's near the site of another Sony factory that made the iconic Sony Trinitron TV.
Pencoed might sound like a remote place to visit, but it's just over two hours from London on the M4 motorway and close to both Cardiff and Bristol airports, making it easy to access from the whole of the UK and Western Europe. Cardiff is Wales' capital city. Now a thriving, diverse, modern metropolis, it is only minutes from the coast and rolling Welsh countryside.
10 year gap
I first visited the Sony site ten years ago and found that while a decade is a long time in the electronics business, the core values remained constant. The first thing you notice is quite independent of the technology. It's that the management values the people that work there. That's not just a platitude: it's borne out by the fact that the company retains staff for an unusually long time - twenty years is quite commonplace, and a few have been there for thirty years.
That length of service leads to an extraordinary depth of experience and expertise. Combine that with the best of Japanese production methods and quality assurance, and it's a formula for success. It has allowed the centre to grow by 10% - 15% annually while keeping its workforce level at just over 600 people. It's the only Sony factory outside Asia and despite the obvious disruption caused by Brexit, it has remained competitive with Asian manufacturers through careful management of people, resources, supply lines and costs.
Sony invited us for a camera launch: a new member of Sony's family of system cameras aimed at broadcast and sports production.
The Sony HXC-FZ90
The HXC-FZ90 is a 2/3"portable studio camera with 4K and HDR capabilities. It is upgradable: the idea is that you can buy the camera now, and it will grow with you. Start with HD, then upgrade with a software licence (permanent, monthly/weekly) to 4K. Even while shooting in HD, you'll benefit from the sensor's natively higher resolution through 4K signal processing and oversampling. It's HDR-capable, and the images on a Sony HDR monitor looked sharp and engaging.
Sony’s new HXC-FZ90 Studio Camera
Another of the camera's talents is producing 4K and HD simultaneously, and it can do the same with HDR and SDR. (Sony has a proven and effective HDR workflow called Sony SR Live). It has 12G-SDI as standard, so no additional hardware is needed to enable 4K live production.
Built entirely in Wales, apart from the lightweight magnesium-cast chassis, the camera is an up-to-the-minute study into how Sony makes high-value, low-production volume equipment. Consumer products sell in large numbers: thousands or even millions. But studio cameras aren't high-volume items, and humans still contribute skills to their final assembly, calibration and testing. Automation, though, is still a critical part of the process.
Putting it all together
Sony's technology centre has its own R&D department tasked with improving productivity, focusing on machine vision. The cameras have thousands of parts, and picking those items and placing them on circuit boards is tricky and laborious. So Pencoed now has a robotic system with machine vision to identify individual components randomly placed on a tray with hundreds of other items. Stereo cameras on the robot's arms scan the parts, and when it "sees" one it recognises, it picks it up and immediately places it on the circuit board. Remarkably, if it doesn't identify any components, it sends an instruction to shake the tray - appropriately with the same Playstation device that generates haptic feedback! Eventually, the robot finds all the parts, places them on the board and sends it off to the next stage.
Some surface-mount components are too small to be individually picked into trays, so they come on a reel, held in place by what looks like plastic or paper tape. Another automated machine, typically fed by three, four or five of these reels in parallel, places the components rapidly and precisely in their place, ready for the flow-soldering machine. Soldering involves "baking" the circuit board so the solder paste melts and fixes the parts. It's a multi-stage process with several independent temperature zones in a linear oven. It's a fine balance between melting the solder and cooking the components, but the process has been fine-tuned over the years to give high yields and a reliable product.
Finally, the finished boards and other parts (like the buttons on the external surface) are ready for final assembly, and surprisingly, that's all done by a single person.
One highly-skilled person does the final assembly, with computerised instructions
Instead of a traditional production line, where individuals or small teams take on specialised, limited tasks, at Pencoed, one person assembles the entire camera. A software assembly manual guides the assembler through each stage, presenting components as needed through a stack of rotating component trays. It's a skilled job that takes years of experience. The advantage of working this way is that it's easier to switch production to a different model when demand changes, and it's efficient, too, because it's not running at the speed of the slowest person in a larger team.
The next stage is to load the camera's software, and from that point on, it's a living system ready for calibration and testing. The calibration process combines new and old technology and is calculated to give extremely accurate and repeatable results. If any camera fails a test, the factory has everything on-site to bring it back to full specification.
Testing is an important part of the process
Added Pi
The Pencoed factory supplements its revenues by making products for other companies, including the famous Raspberry Pi ultra-low-cost computer. Production for this tiny board is almost entirely automated and includes packaging to leave the product ready for shipping. Entirely by coincidence, I'm sure, one new Pi is produced approximately every 3.14 seconds.
The Sony Technology Centre in Pencoed discovered the essence of its operating philosophy years ago: put people first, and the rest will follow. That doesn't mean it's easy. The factory's processes are still evolving - and always will, to keep pace with technology. It has weathered the Brexit friction, the Covid crisis, and the extraordinary rate of change. Like the cameras it carefully builds, Pencoed does its job quietly, modestly and brilliantly. And, a decade since I first visited, it feels like it has more than earned its place in the company of the Asian technology giants.
Tags: Production
Comments