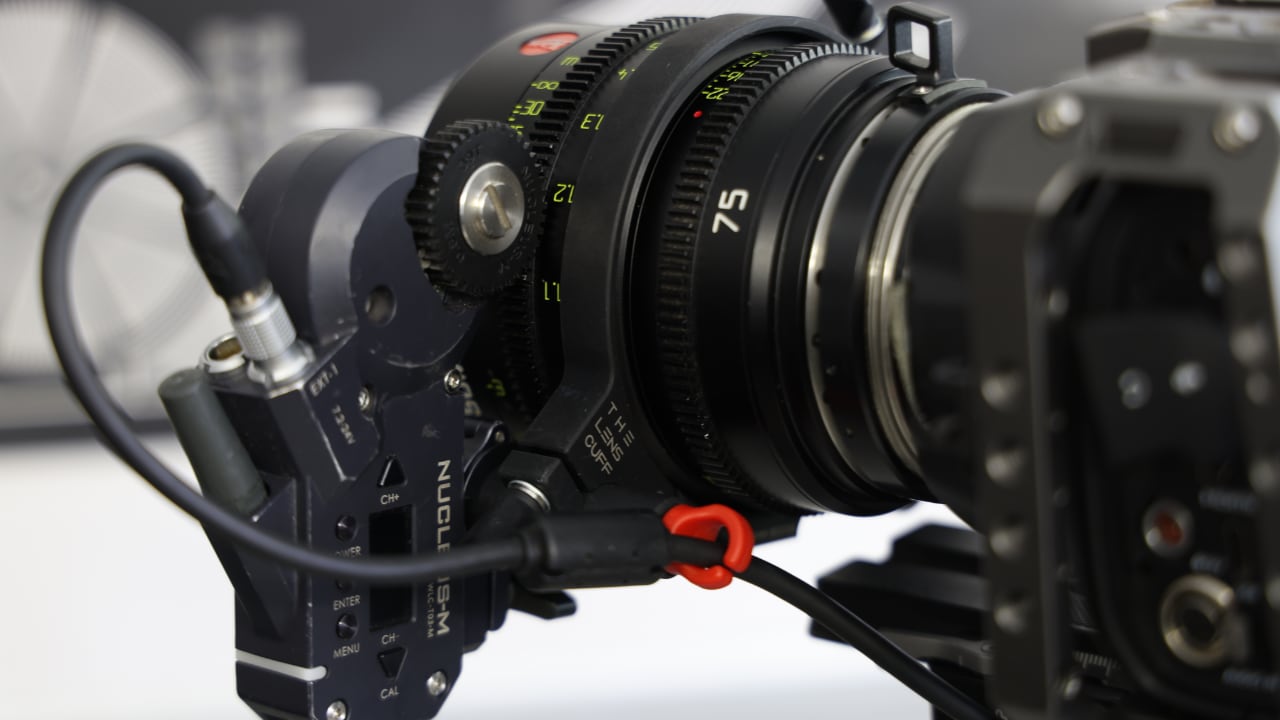
We need to torque: A new invention allows you to mount follow focus motors directly onto a cinema lens.
Follow focus motors are quite obviously a great idea but they are also often quite problematic. Which is why last month, Corfu-based VFX artist and Cinematographer Gregory Karydis finally started selling The Lens Cuff, completing a five year journey since he first had the idea.
"This is a solution to a decades long problem in the industry where lenses and lens mounts are torqued and "tortured" by remote follow focus motors, leading to issues such as skipped gear teeth, out of focus images, tortured vintage lenses, damaged lens mounts and "bumped" footage," he explains. "All of this requires reshoots that can be as simple as everyone going back to their marks, to more complex, such as resetting a scene, bringing a camera down from a drone, jib or car rig for re-calibration, to rebuilding entire sets that take time and cost a lot to a production. And that's if this is noticed during a shoot."
He first started to play with the idea of solving the problem in 2018. The basic concept was to move the mounting point of the follow focus motors from the base or somewhere around the camera body to the lens itself. This would effectively make a closed system that was no longer affected by external forces, while equally it would not provide any force inputs into the camera or the surrounding system.
Like with many other creative projects, it was during the pandemic lockdowns that it really started to pick up "when we were forced to stay at home with my expectant wife staring at my new 3D printer wondering what to do... And in one evening, armed with patience and a lot of inspiration, I came up with the current shape and form."
That current shape and form is nowadays made of materials way in advance of what you can do with a 3D printer and serves as a mount for the follow focus motors by providing a low-profile lens support foot with 1/4 20 thread and ARRI Standard orienting pins alongside symmetrical 2x 15mm rail clamps. In fact it's made from a single block of aircraft grade Aluminium 6082 and available in five adaptable sizes, from 65mm to 114mm.
It requires at least 10mm (3/8′′) on a non-moving segment of the lens body. Karydis says that ideal placement is between the Focus, Iris or Zoom rings, but anywhere where the barrel is genuinely tubular will work.
Up to three motors can be attached. It is recommended to position up to two motors on each side of Cuff. "Ideally, go for symmetry," he says. "If it’s a prime lens, one on each side for Focus and Iris. If it’s a zoom lens, two on one side and the third one on the other. It won’t affect the performance but it will affect the balance of your setup."
Pricing starts at $395 for a single unit with deals available as you buy more.
Tags: Production Lenses
Comments